El seminario técnico organizado por la Asociación Nacional de
Industriales de Aceites y Mantecas Comestibles, A.C. (ANIAME) y la American
Soybean Association (ASA) en la Ciudad de México el pasado 27 de septiembre,
destacó la importancia de renovar tecnologías en la producción
y refinación del aceite de soya y abrió el debate en cuanto a
la definición de calidad y la posibilidad de producir biocombustiblesen
México.
La primera sesión dedicada al impacto de la calidad de soya sobre la
producción de pasta y aceite, a cargo del Ing. Pedro González de
la Asociación Americana de Soya, hizo referencia a la necesidad de eliminar
los ácidos grasos trans, contar con parámetros más confiables
para medir la cantidad de tocoferoles y esteroles, menos polímeros glicéridos
oxidados, sustancias que pueden ser cancerígenas, y contaminantes en
la semilla.
Hoy en día los procesos de deodorización se realizan a partir
de la destilación con vapor, el proceso más costoso, y para cambiarlo
por amoniaco, es necesario un diseño del equipo y la maquinaría
más acorde con las necesidades del productor y contar con nuevas soluciones
a problemas específicos. En cuanto a la automatización del equipo,
se sabe que existe mucha ciencia detrás de estos diseños porque
pueden eliminar o aumentar ciertas sustancias, porque ahorran tiempo en todo
el proceso, o bien, cuentan con diferentes equipos para diferentes aceites.
Todo esto es necesario para garantizar la mejor de las calidades posibles y
que la empresa sea competitiva a nivel internacional.
El Dr. Adolfo Subieta de DeSmet Ballestra en Estados Unidos,
se refirió a la producción de biodiesel con aceite de soya y
canola, como una posibilidad de expansión de la industria aceitera actual;
especialmente, en Estados, Europa y algunos países de América
Latina.
En los últimos años se han construido plantas integradas con
silos, tanques y refinadoras a fin de ahorrar costos de producción.
En cuanto a las normas de seguridad, el Dr. Subietea señaló que
en las plantas de biodiesel, todavía no existe un equivalente en normas
de seguridad como las que tienen las plantas aceiteras. De gran importancia
es la logística dentro y fuera de la planta: que cuente con vías
ferroviarias cercanas y puertos de embarque.
En un principio se pensó que las plantas de producción de biodiesel
podían ser pequeñas, de unas 15,000 toneladas; sin embargo, la
realidad mostró otra cosa y hoy existen plantas que producen de 50 a
900 mil toneladas; por ejemplo, en España DeSmet Ballestra diseña
la planta sin olvidar el proceso químico, con niveles de automatización
eficientes, y equipos que trabajan con líquidos y vapores con gran experiencia
tanto en la industria química del petróleo como aceitera, aunque,
por supuesto el biodiesel es un negocio con características diferentes.
El Dr. Subiera afirmó que aún con toda la producción
mundial de oleaginosas, se lograría producir sólo el 2% de los
requerimientos mundiales de combustibles, y por esa razón, está habiendo
un acercamiento entre la industria petrolera y la de biodiesel, un tema de
suyo controvertido, ya que la opción está entre producir alimentos
para muchos millones que todavía no cuentan con suficientes o bien,
la producción de energéticos más eficientes y que ayuden
a reducir la emisión de gases contaminantes a la atmósfera.
Se ha comprobado que el aceite de canola es el más adecuado para producir
biodiesel y es el que, junto con la soya, se está utilizando en Europa;
pero en Canadá, un gran productor de esta semilla, más bien se
destina a la exportación. La interrogante de los biocombustibles está abierta –señaló el
Dr. Subiera- junto con el precio, porque si uno tiene que consumir aceite de
canola, tiene que pagar un precio más alto. Por supuesto se han buscado
alternativas, entre las que destaca el uso de pastizales, la jatrofa no-comestible
y algas marinas naturales y cultivadas con sistemas de acuacultura, recursos
que no compiten con semillas comestibles. Es todavía una incógnita
que es lo que va a alimentar a estas fabricas de biocombustibles, puesto que
la materia prima representa el 80% del costo total y, por ello, ya han surgido
los especuladores, especialmente en España y en Estados Unidos que acaparan
el aceite y por esa razón, ha subido el precio. Cada galón que
producen, pierden dinero, al grado que muchas plantas han tenido que cerrar
sus puertas. Y, aunque la producción de biodiesel es un negocio rentable,
no lo es en las condiciones actuales.
Para un mayor rendimiento es necesario tener materia prima adecuada, al precio
más adecuado. La glicerina es, hasta el momento, el principal subproducto
que representa el 10% pero no cuenta con un mercado estable. Por esta razón,
los investigadores trabajan en la búsqueda de nuevos subproductos más
rentables. La transesterificación química es el proceso más
eficiente, y desde el punto de vista químico no hay problema; del aceite
se obtiene metanol o etanol, y finalmente biodiesel y glicerina, pero el proceso
es más complicado que en el laboratorio, porque las gomas, el agua y
los jabones afectan la reacción.
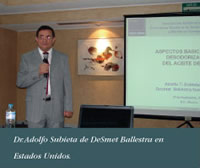 |
¿Puede utilizarse cualquier aceite? Si, pero sin perder el punto de
vista de máxima calidad al menor costo. Esto es lo importante. El aceite
RBD produce biodiesel y glicerina de buena calidad. En cuanto a las normas,
en Europa y Estados Unidos existen unas 600. Desde el primer momento es necesario
tratar de obtener glicerina de buena calidad, pues aunque por el momento no
es muy rentable, cuando se abra el mercado, ya no habrá posibilidad
de revertir el proceso, o al menos, costará más dinero y más
trabajo.
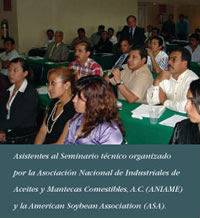 |
Los parámetros críticos se fundamentan en la seguridad, especialmente
de todos los equipos eléctricos. Por ejemplo, tienen que estar a prueba
de explosión y tienen que seguir una larga serie de pruebas. Los químicos
tradicionales no pueden trabajar en las plantas de biodiesel, porque tienen
que ser especializados con procedimientos computarizados, automatizados y rápidos.
En la primera planta de biodiesel que DeSmet Ballestra montó, estuvieron
los ingenieros de Bélgica, y aún así, como los procesos
son muy rápidos, cuando menos lo esperaban, ya tenían materia
prima de poca calidad. Es importante que el equipo esté funcionando
en forma continua, más de 8000 horas al año, con suficiente materia
prima, almacén y transporte. Es necesario diseñar una economía
de escala y procesos de transformación de aceite comestible en biodiesel,
puesto que a mayor producción, menor costo.
El Ing. Víctor Villa Salinas de SudChemie de México,
desarrolló el tema del blanqueo, técnica indispensable
para que todo el proceso alcance la mayor eficiencia posible, que se traduce
en calidad de aceite, que de suyo es un alimento y un vehículo para
producir otros alimentos. Es necesario medir la calidad en cuanto a parámetros
tan abstractos como la salud, aprovechamiento nutricional, sabor, olor, estabilidad,
costo. Así mismo, se mide el contenido de tocoferoles: alfa tocoferoles
y vitamina E / esteroles. Con un blanqueo eficiente es posible eliminar hasta
niveles mínimos los elementos de oxidación con máxima
estabilidad.
Entre más polinsaturado sea un aceite, más riesgo de oxidación.
Por eso, no es posible seguir el mismo procedimiento para todos los aceites.
Es necesario medir la clorofila, promotor del proceso de oxidación.
El “blanqueo térmico” (rojo-verde) es una técnica
que ayuda a medir y eliminar el contenido de clorofila en el aceite. La calidad
se mide a partir del valor de peróxido, valor de anisidina, valores
que el consumidor industrial puede detectar y, por supuesto reporta esta anomalía
al productor, por lo que es necesario cuidar al máximo todo el proceso
de blanqueo a fin de reducir los precursores de la oxidación del aceite.
El Ing. José Becerra Riqué, consultor independiente,
hizo una muy completa lista de pruebas de calidad para aceites y mantecas,
desde la recepción de materia prima, hasta su lanzamiento al mercado.
Destacó la importancia del almacenamiento, reducción de fósforo
y fierro, así como la formulación, deodorización y blanqueo.
El control de efluentes y agua residual debe constituir hoy una rutina de control.
En calidad, los análisis se hacen en forma cotidiana y continua: cada
ocho horas, cada semana, otros cada quince días, o cada vez que sea
necesario, con muestras representativas y siguiendo las pruebas desarrolladas
por la ADCS. Existen pruebas sensoriales como la degustación, visual
como el color, y organolépticas. Cada lote se marca con una clave especial.
En las pruebas de calidad se incluye la formulación de nuevos productos,
la posible contaminación de líneas y de equipo, análisis
de control para cada producto terminado; por ejemplo, la manteca hidrogenada
de soya 37-38, ya que todavía en México una prueba de control
de la cantidad de ácidos grasos trans. Hasta la fecha se siguen los
parámetros de Estados Unidos; aunque ya hay presión para evitar
que cada fabricante establezca sus propios criterios. Existen también
pruebas funcionales, para procesos específicos como el freído,
horneo, aderezos, vida de anaquel, cremas para relleno, y otras.
El Ing. Fernando Maya, consultor de la Asociación
Americana de Soya, México habló de la importancia de los envases
para aceites que hoy en día utilizan el Pet. Cada botella de
aceite utiliza 30gr de Pet. Los aceites, a diferencia de otros productos requieren
de cajas especiales y la estibación adecuada elimina el riesgo de la
botella se colapse o se derrame el aceite. Ya existen normas para el proceso
de envase, almacenamiento y transporte de aceites muy precisas. Por ejemplo,
la prueba de integridad para el soporte de cargas, fuga, que en envase se colapse
o se deforme. La prueba de vibración que mide huellas de abrasión.
La prueba experimental de posibles fugas y consiste en arrojar el envase en
caída libre desde una altura determinada y es apta para manejo rudo.
ANIAME © Copyright 2007
Praga 39 Piso 3, Col. Juárez. Delegación Cuahutémoc
C.P. 06600 T. 5533-2847 F. 5525-7551 |